20 - 01 - 2022
Written by BPTW Architectural Partner and sustainability lead, Neill Campbell, in collaboration with Certified Passive House Designer Dido Graham.
Fuel poverty is a serious issue in England with 13.4% of households considered fuel poor in 2019 according to the most recent Government statistics (1). The built environment contributes around 40% of the UK’s carbon footprint, half of which is attributed to operational uses (2). Houses designed to Passive House standard can provide energy savings of up to 90% compared with typical building stock and 75% for new builds (3), offering homeowners and tenants significant energy savings that can help reduce fuel poverty. So why don’t we build more Passive House homes?
The benefits of Passive House are well recognised by local authorities and housing associations in England. This understanding has been further supported by the Passivhaus Trust’s Passivhaus Social campaign that promotes the adoption and implementation of the Passive House Standard in affordable housing design. Despite this, social housing providers are still facing many barriers in the delivery of quality, affordable and sustainable homes. This article assesses why such obstacles persist and identifies how these difficulties can be overcome in the journey towards building better homes in the UK.
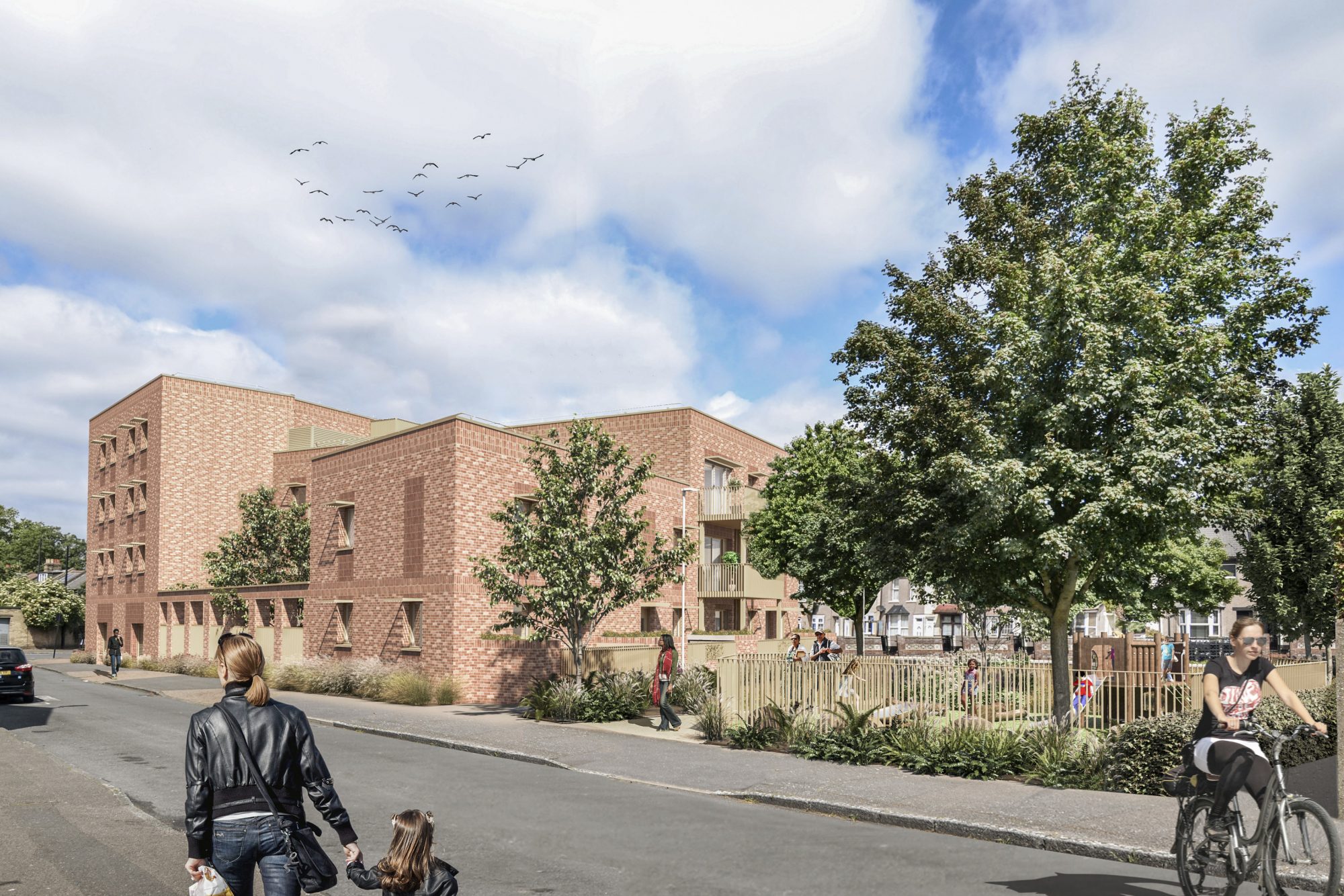
The basis of Passive House
The first Passive House home was built 30 years ago in Germany (4). Despite its age, the house continues to perform as it did on the day it was completed, providing construction professionals with 30 years of data to confirm how the Passive House model offers energy efficient, comfortable, and cost-effective homes. The most common Passive House housing typology in the UK is a standalone house built by a private owner. Unlike on the continent, in the UK multi-dwelling homes such as apartment buildings designed and delivered to Passive House standards are rare. Although, they have recently increased in popularity as a result of exemplar developments such as the 2019 Stirling Prize-winning Goldsmith Street by architects Mikhail Riches.
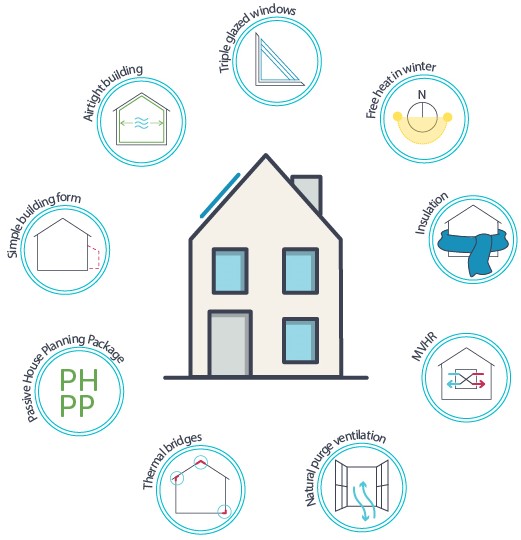
In its most basic form, Passive House is the balancing of energy gained and energy lost from a building. It is achieved by creating an incredibly efficient building envelope that eliminates losses through surfaces and air while using a mechanical system to provide clean, fresh air to the building without heat loss. This is achieved by considering five principles in the design:
- Air tightness
- Highly insulated thermal envelope
- Triple glazed windows
- Thermal bridge-free construction
- Adequate ventilation systems
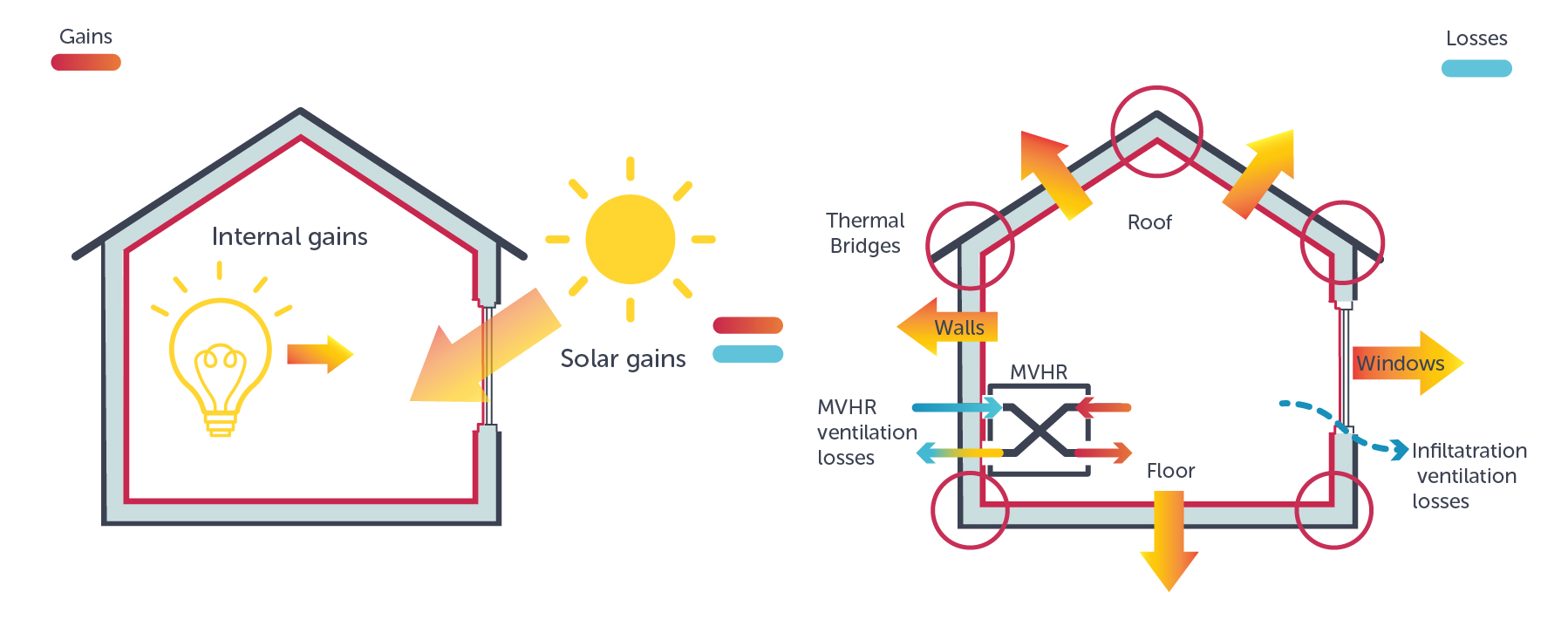
The balancing achieved with these five principles enables the building to use less energy to run (75% less in comparison to the average new build) because the energy inputted to heat the building does not leak out. Therefore, making the overall running costs of the building lower and cheaper for the users. Additionally, a certified consultant will track and balance the elements and conditions of the building from the design stage to completion and certification, using a live modelling tool called a Passive House Planning Package (PHPP) alongside on-site checks.
Passive House in use
Surprisingly, when we look at studies of in-use buildings constructed to current building regulations standards rather than Passive House we are confronted with a performance gap of between 10-150% above what the notional condition should be (as defined by building regulations). This is largely the result of heat being lost through the building’s fabric (6).
On top of balancing energy use and loss, energy generation and fossil fuel-free energy sources are also considered in the Passive House standard and there are grades of the standard that require differing levels of renewable energy production on site, such as classic, plus, and premium (7).

Obstacles to Passive House homes in the UK
In theory and practice Passive House appears to be an excellent way of designing low-energy, fuel-saving buildings, so what is hindering its use?
There are perpetuating myths about Passive House buildings that can largely be disproved but that continue to affect the industry’s perception of Passive House projects. These include cost, certification and ventilation.
Myth 1: “It is 25% more expensive to build to Passive House standard than current building regulations.”
Yes, there is a construction cost uplift associated with the building fabric cost of Passive House buildings. However, in general this additional construction cost is between 3-8% more than equivalent normalised projects (8). This increase in cost can be recouped through the running costs of the building being considerably lower. The quality of the build also means that the longevity of the building is better.
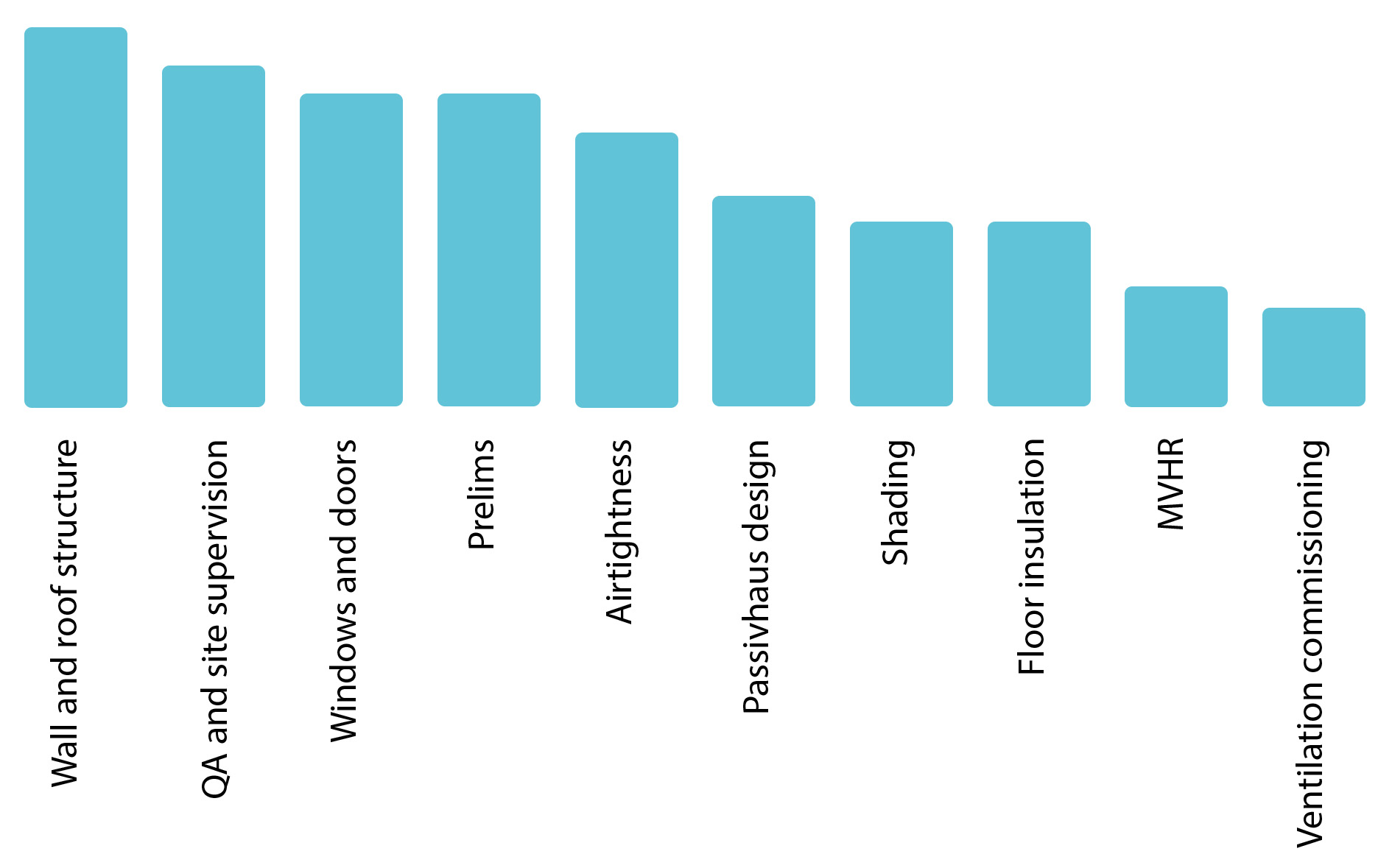
Myth 2: “All elements of the building must be Passive House Certified products.”
While this can be beneficial, only the MVHR system needs to be Passive House certified for a building to be to Passive House standards. This is to ensure that the MVHR system meets the required efficiency ratings. All other building elements should only meet the specification necessary for the PHPP modelling. There is a cost uplift associated with products that have paid a fee to put the certified stamp on their products. This can be avoided by specifying uncertified but high-quality components that meet the required standards.
Myth 3: “You can’t open the windows in a Passive House building.”
This is incorrect. Windows can be opened for natural purge ventilation as normal and, where possible, Passive House homes are designed to be dual aspect to enhance natural ventilation. The benefit of the Passive House approach is that when the windows are closed, clean, fresh air is still supplied, relative humidity levels are maintained, pollutants are removed from the internal environment and the background MVHR keeps the heat inside the building. In warmer seasons, the fabric of the building also helps to keep the heat out so there is less need to open windows for cooling. A Passive House building will operate at a consistent temperature all year round.
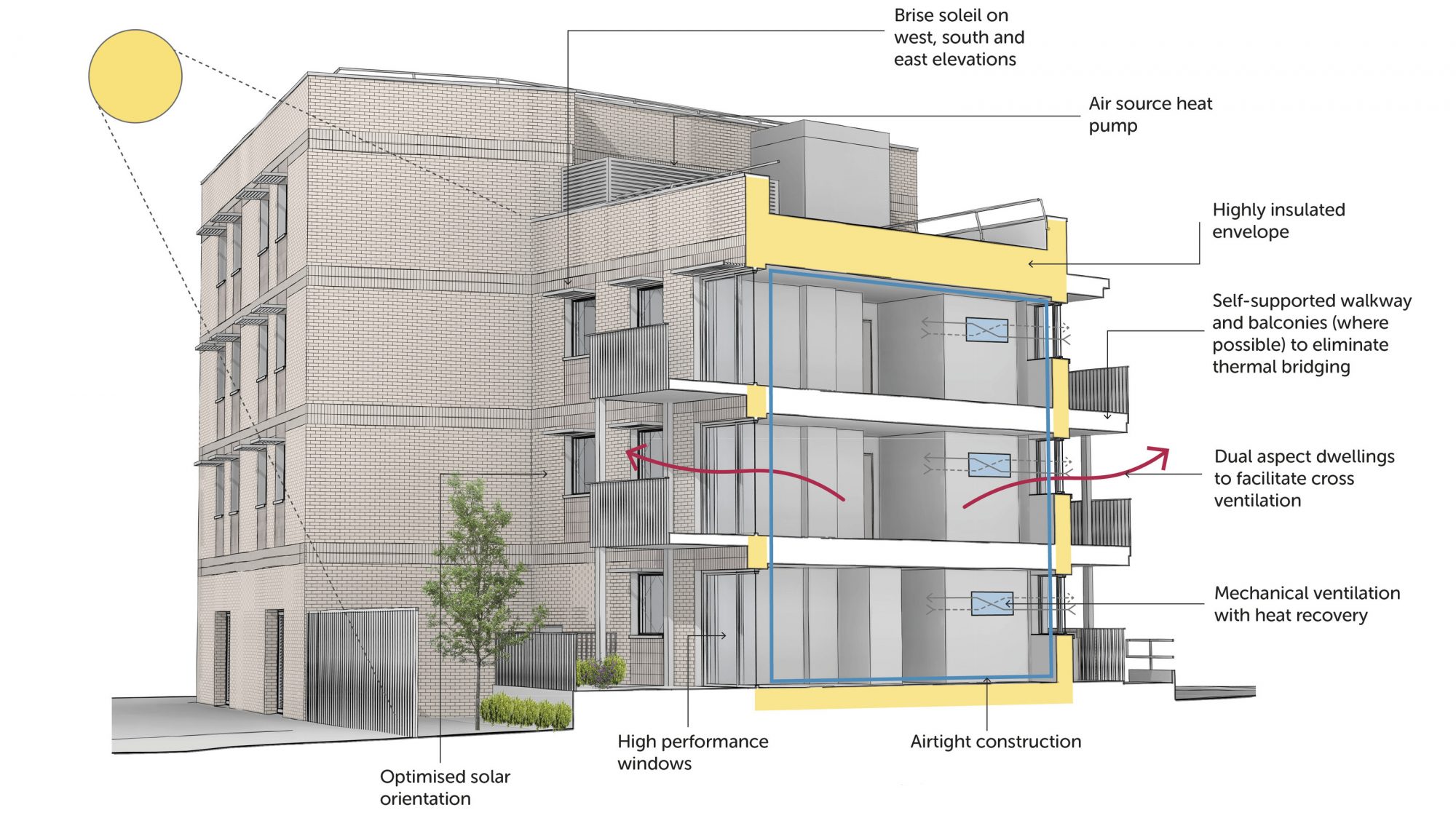
Myth 4: “Air source heat pumps will make everything cheaper.”
Currently, electricity is significantly more expensive than gas. The electrical grid in the UK also has less capacity than the gas infrastructure. Therefore, substantial changes are needed to the cost and supply of electricity for air source heat pumps to be cost effective if all buildings are to switch to this heating method. On the other hand, the fabric of a Passive House building is incredibly efficient. This means less energy is used to heat and run the building, and the energy bills are lower as a result. Unfortunately, if an air source heat pump is used in a leaky, Victorian terrace it would be considerably more expensive to run and would struggle to adequately heat the house.
Myth 5: “If you start the processes, you must hit the target and become certified.”
It is possible to design to the principles of Passive House standards without certification. In an ideal world certification would be achieved because it provides a mechanism to track performance. However, if there are constraints that prevent a project from achieving the full standard the Low Energy Building Standard can be used instead (9). This allows the quality and intent of the project to be maintained without gaining full certification.
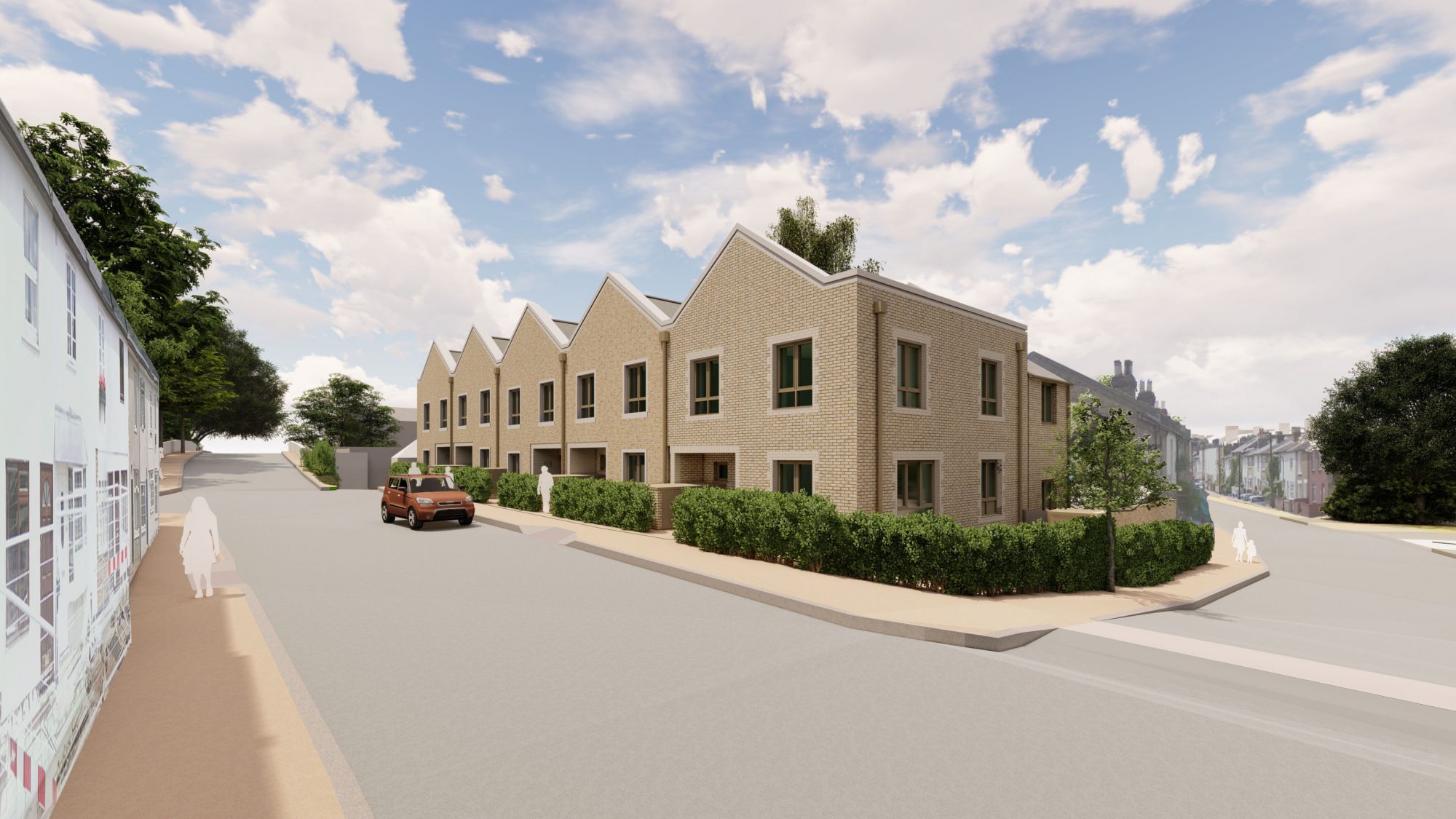
The greatest challenge? The uptake of Passive House
Having discussed some of the myths associated with Passive House that can be simply disproven, the main hurdle to a Passive House development is the idea of cost uplift. Most councils and housing authorities are working on an extremely tight budget where cost increases can make or break a project, so efficiencies in cost need to be seriously considered.
With traditional design and construction methods, value engineering and efficiency audits are often carried out on projects to achieve savings with meticulous cost analysis during the early pre-planning stages. With private individual houses the initial construction uplift associated with Passive House can be balanced against the reduced running cost of the building, but for social housing providers and multi-home developments this payback is not felt by the provider. Therefore, a cost to build increase is less appealing.
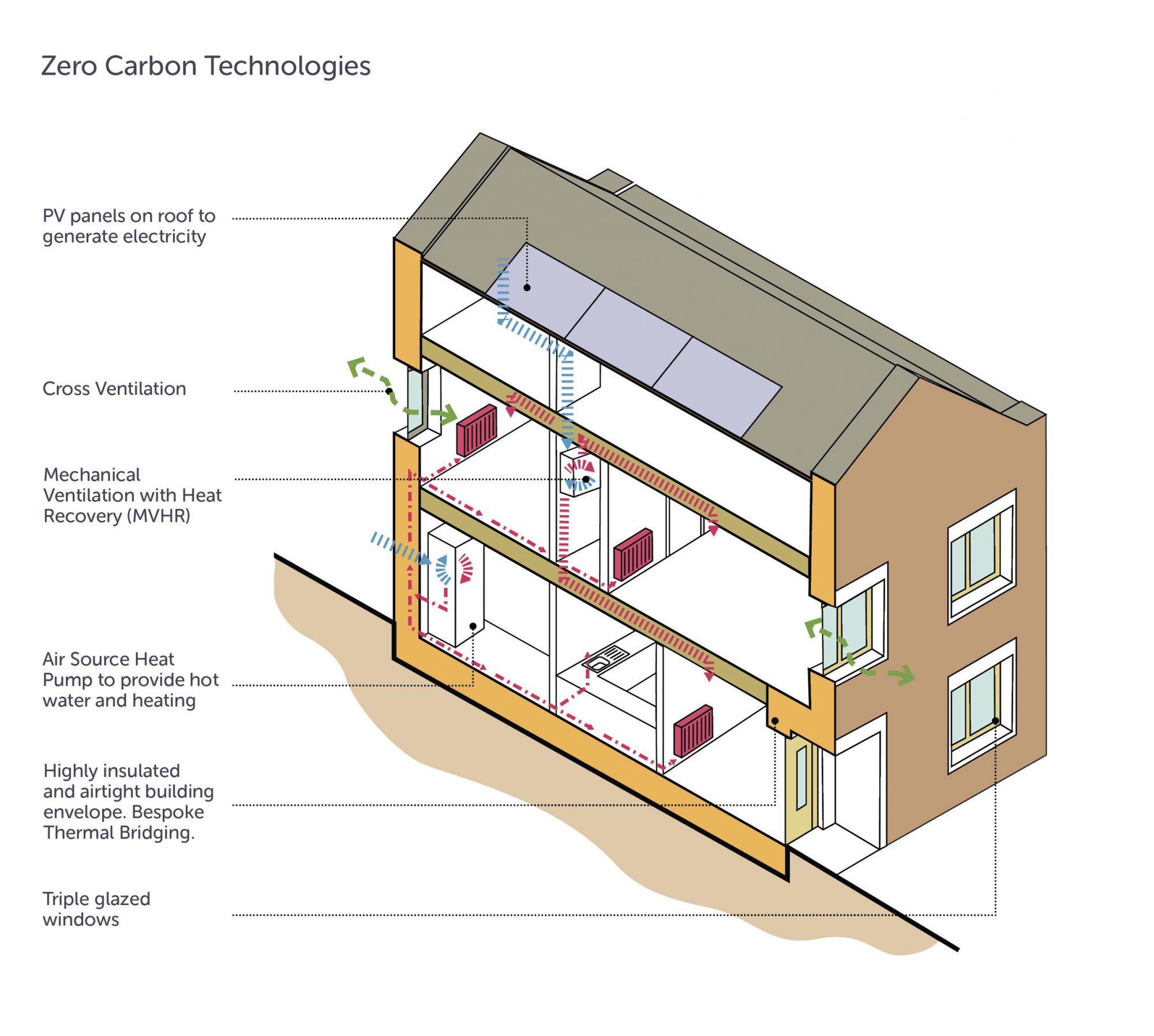
Value engineering is also limited in Passive House projects because the construction components must be to a very high standard. Some savings can be made by choosing uncertified products that meet the same performance levels, but this type of “value engineering” does not deliver the substantial financial savings that can sometimes be achieved on non-Passive House projects – that being a cost saving attained often at the expense of build quality. Despite this, there are a few areas where opportunities for financial savings can be made which we will examine in more detail below along with possible solutions to the economic issues.
Timing
Deciding to deliver a Passive House scheme after planning or late on in the design stage will increase the cost of the build.
There are some key design principles that need to be ingrained in the design from an early stage to avoid cost increases. These are largely the same considerations that will help reduce the cost of any design, including principles of simple building form and efficient organisation of programmes within the building. By maintaining a low form factor (the ratio between the area of the external envelope divided by the treated floor area of the building) and the principles of balancing the gains and losses of the building from an early stage the cost of the delivery will be less. This is because a larger surface area has greater potential for heat loss. To counter act the heat lost through a large surface area, the thermal capacity of the building fabric will require higher specification components and increased costs for thermal bridge analysis. Therefore, creating a more complicated build.
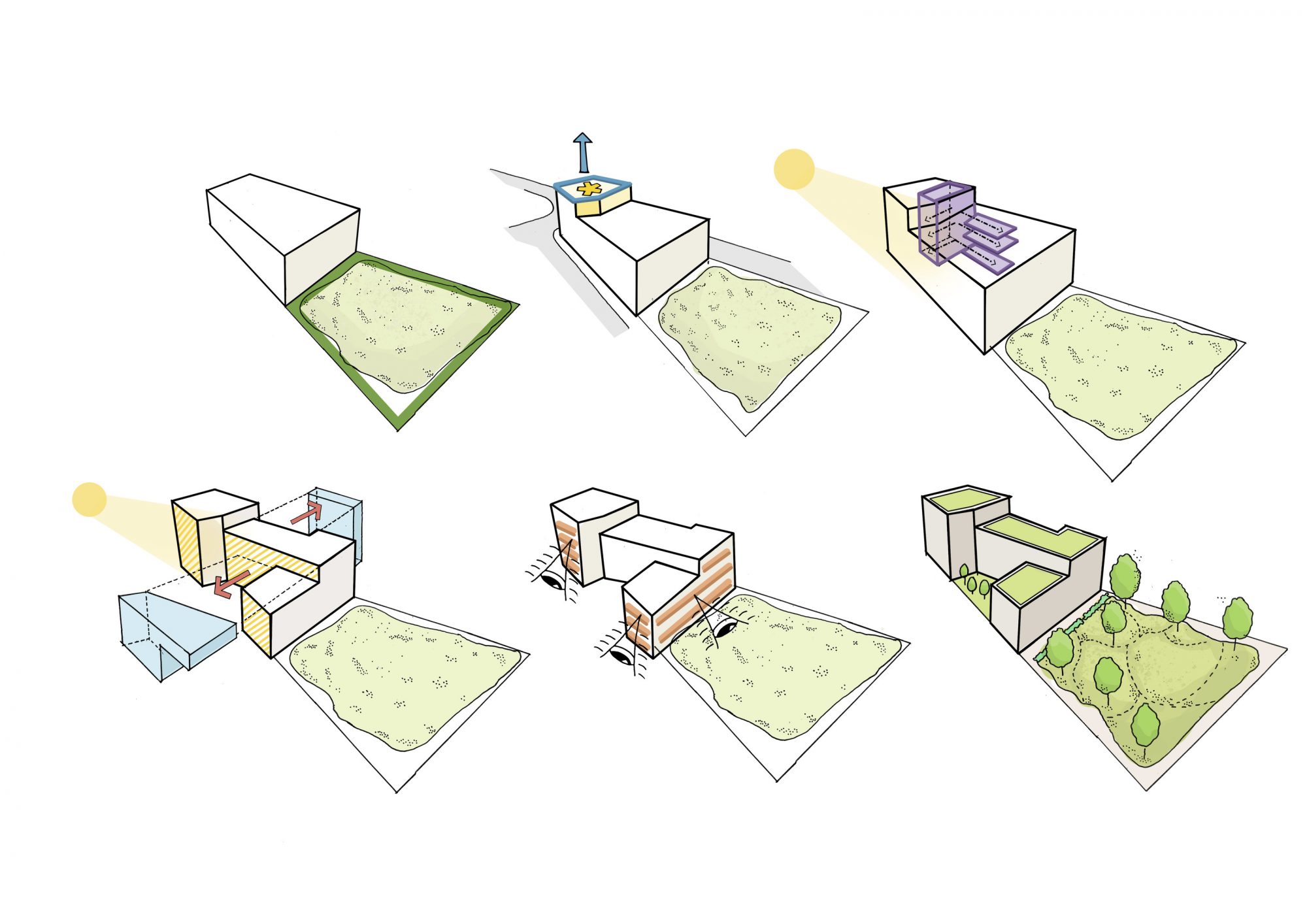
We aim to help the client make the decision to deliver their schemes as Passive House in the very early stages of the design and use the principles to inform design decisions from day one. Over time this methodology will help alleviate unnecessary costs associated with designing to Passive House standards. Especially, as we move towards Net Zero Carbon standards which are closely aligned with the energy requirements in Passive House .
Experience
A lack of industry knowledge about Passive House generates a perception of risk and expense that is transferred to the client in increased quotes at the tender stage.
There are still only a few large contractors that have delivered large-scale housing developments to Passive House standards in the UK. Therefore, the knowledge and expertise gained from delivering such projects is focused within a few companies. Furthermore, the design processes were variable with Passive House standards implemented later in the design process for some, resulting in increased costs and complicated delivery processes. It could be that these discrepancies are being reflected in the construction cost quoted by contractors who have constructed these projects.
One passive solution for this is time. As more schemes are built the price will reduce naturally and this is something that can be seen today. The Passive House Trust’s 2015 study suggested a cost uplift of 15-20%, concluding that this was associated with Passive House’s innovative nature, but in 2019 the cost had fallen to 8%. A further reduction to 4% or less is predicted as it becomes adopted at scale. However, many clients are not willing to accept the risk associated with Passive House’s “research and development” approach, so another solution must be sought to bolster its uptake.
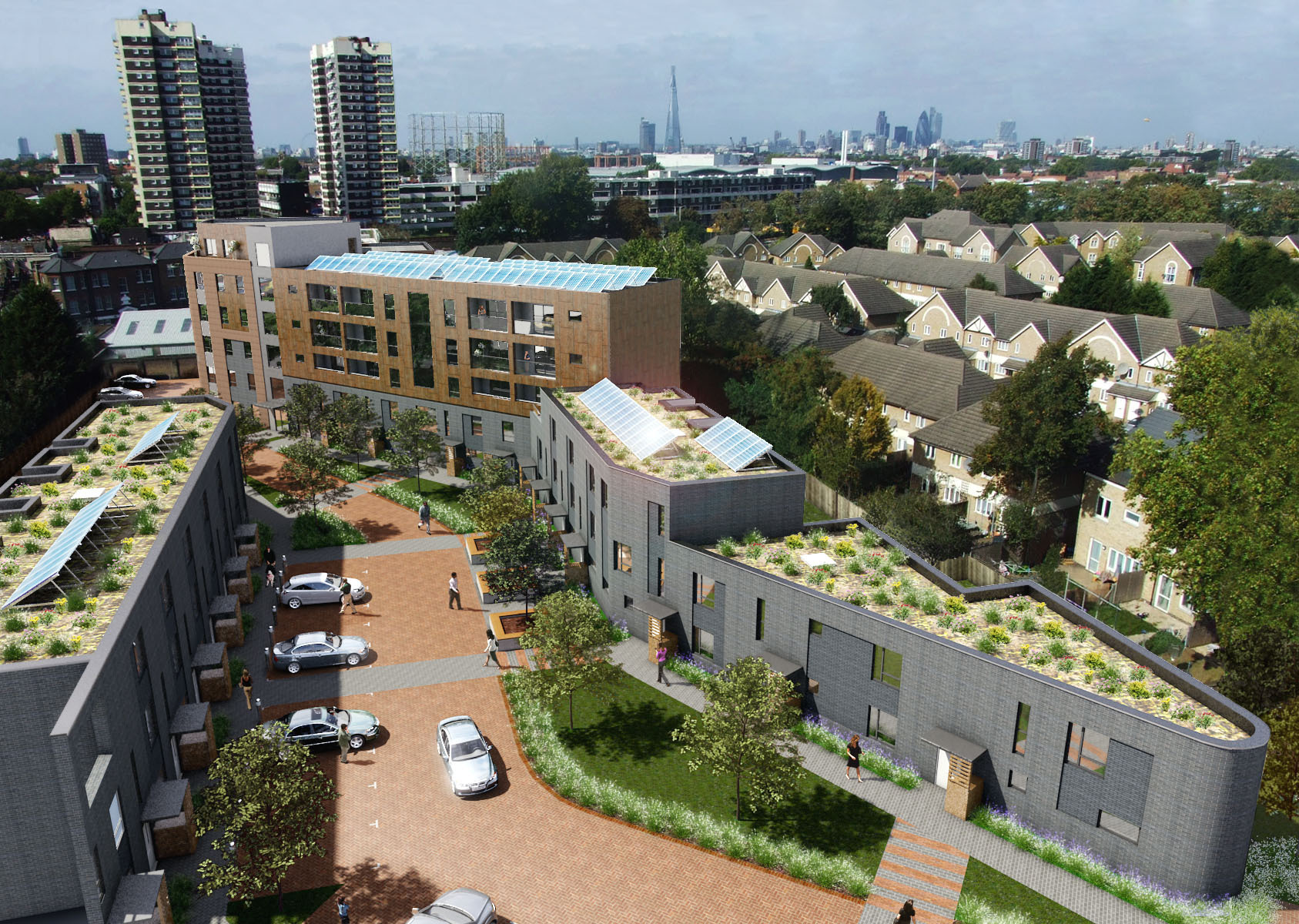
Research and development
There is a deeper problem that represents a fundamental hinderance to the uptake of Passive House in the UK. As indicated in the 2017 Farmer Review, the UK is experiencing a problem with innovation, training and research and development in the construction industry (10).
Passive House, although not entirely new at 30 years old, requires a different way of looking at buildings and construction. There is a lack of government-funded training for contractors that could facilitate a faster decrease in the costs associated with Passive House delivery.
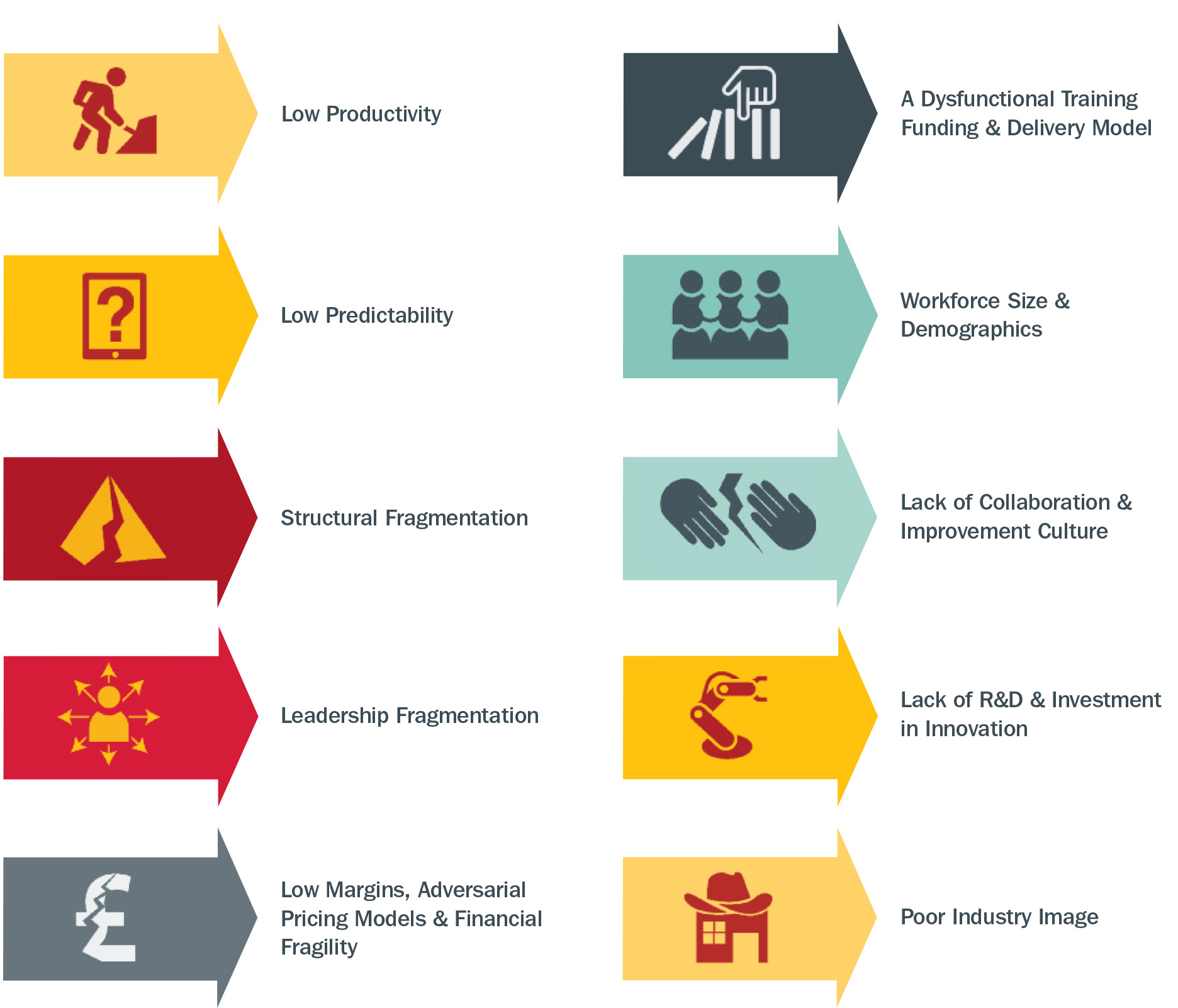
We are behind the curve with Passive House in the UK, and in many ways also with our ambition for net zero carbon. If we look to the continent, we see the NZEB standard which has similar ambitions to the UK’s net zero carbon. However, the NZEB standard is supported by a training infrastructure that is subsidised by governments and the EU (11). In contrast, the UK offers piecemeal training associated with individual organisations such as AECB, Passivhaus Trust and private organisations with Passive House accreditation. If we are to meet the ambitious target of net zero by 2035, a similar considered approach needs to be implemented in the UK.
To see a meaningful decrease in construction costs for Passive House projects we need more joined up thinking between the industry and Government ambitions alongside more industry pressure for Government funded training.
Key takeaways
The economic uplift is the primary barrier to the use of Passive House and true net zero carbon in the UK. As we have discussed, much of this uplift can be alleviated through careful design from the start. However, some of the economic uplift is currently unavoidable and created as the industry transitions to this new and better way of constructing buildings. We are likely to see this uplift decrease over time but unfortunately, more clients need to take the leap to allow this decrease to happen faster – whilst also benefiting from the other positive aspects of the approach.
The built environment contributes to around 40% of the UK’s total carbon footprint, with half of this created by operation uses (12). It is clear that the impact of the construction industry is great and that it is a contributing factor to the rising global temperatures. To combat this, building techniques need to be updated to reduce the carbon emissions associated with constructing and running buildings. Following a fabric first construction approach like Passive House and net zero offer this opportunity.

Our hope is that the benefits of alleviating fuel poverty through well-designed buildings will encourage our clients to see past the current increased delivery costs to the necessary future position which Passive House and net zero design can deliver. Architects have a role in designing better projects more efficiently to increase confidence in the Passive House methodology and thereby lower construction and delivery costs.
There is of course a wider industry issue surrounding a lack of training and a skills gap which could be addressed through government-led training schemes and incentives to encourage contractors and consultants to learn how to deliver Passive House projects efficiently. The training provided by the Passivhaus Trust and other private organisations can only go so far in plugging this knowledge gap.
Reflections
This article aims to highlight how despite the challenges, Passive House and net zero building techniques can deliver more comfortable, cheaper to run and healthier homes. While the current cost uplift of this methodology is greater than traditional methods, the benefits to residents and society can be seen to outweigh the initial cost uplift. 2021 has seen much turbulence, but it is possible to be hopeful that many of the issues raised here will be addressed in the coming years encouraged by regulation changes from 2022 and the fallout from COP 26. In all, we are reminded of the main focus of these improvements: better homes for people to live in.
Neill Campbell is a Partner at BPTW and leads the sustainability working group. As a result of his extensive experience of council housebuilding, Neill regularly presents to professional bodies, such as the NLA, The Housing Forum and Future of London, on the development potential of residential sites across London and the South East. He also represents BPTW on Future of London’s Council-led Housing Forum.
End notes
- Business for Business, Energy and Industrial Strategy’s ‘Consultation on the Fuel Poverty Strategy for England’ dated 16 September 2019.Available here: Fuel poverty strategy for England: consultation (publishing.service.gov.uk)
- UK Green Building Council’s “Climate Change”. Available at: Climate change – UKGBC – UK Green Building Council
- Passive House Institute’s “25 Years Passive House”. Available here: Passivhaus Institut (passivehouse.com)
- Passipedia’s “The World’s First Passivhaus Home” dated September 2020. Available at: The world’s first Passive House, Darmstadt-Kranichstein, Germany [ ] (passipedia.org)
- Encraft’s Technical Insight “Whole-life Costs of a Passivhaus” dated February 2014. Available here: WLCA: Whole-life costing analysis for domestic Passivhaus buildings (passivhaustrust.org.uk)
- Innovate UK’s ‘Building Performance Evaluation Programme: Findings from domestic projects. Making reality match design” dated January 2016. Available here: https://eprints.leedsbeckett.ac.uk/id/eprint/1054/
- Passipedia’s ‘Classic, Plus, Premium: The new Passive House classes and how they can be reached’ dated January 2021. Available here: Classic, Plus, Premium: The new Passivhaus classes and how they can be reached [ ] (passipedia.org)
- Passivhaus Trust’s ‘Passivhaus Construction Costs’ dated October 2019. Available here: Passivhaus Construction Costs (passivhaustrust.org.uk)
- Passive House Institute’s ‘Criteria for the Passive House, EnerPHit and PHI Low Energy Building Standard’ dated August 2018. Available here: 03_building_criteria_en.pdf (passiv.de)
- The Farmer Review of the UK construction labour model dated 2016. Available here: Construction labour market in the UK: Farmer review – GOV.UK (www.gov.uk)
- Training courses offered by NZEB. Available here: Train-to-NZEB: The Building Knowledge Hubs | Train-to-NZEB Project | Fact Sheet | H2020 | CORDIS | European Commission (europa.eu)
- UK Green Building Council’s “Climate Change”. Available at: Climate change – UKGBC – UK Green Building Council